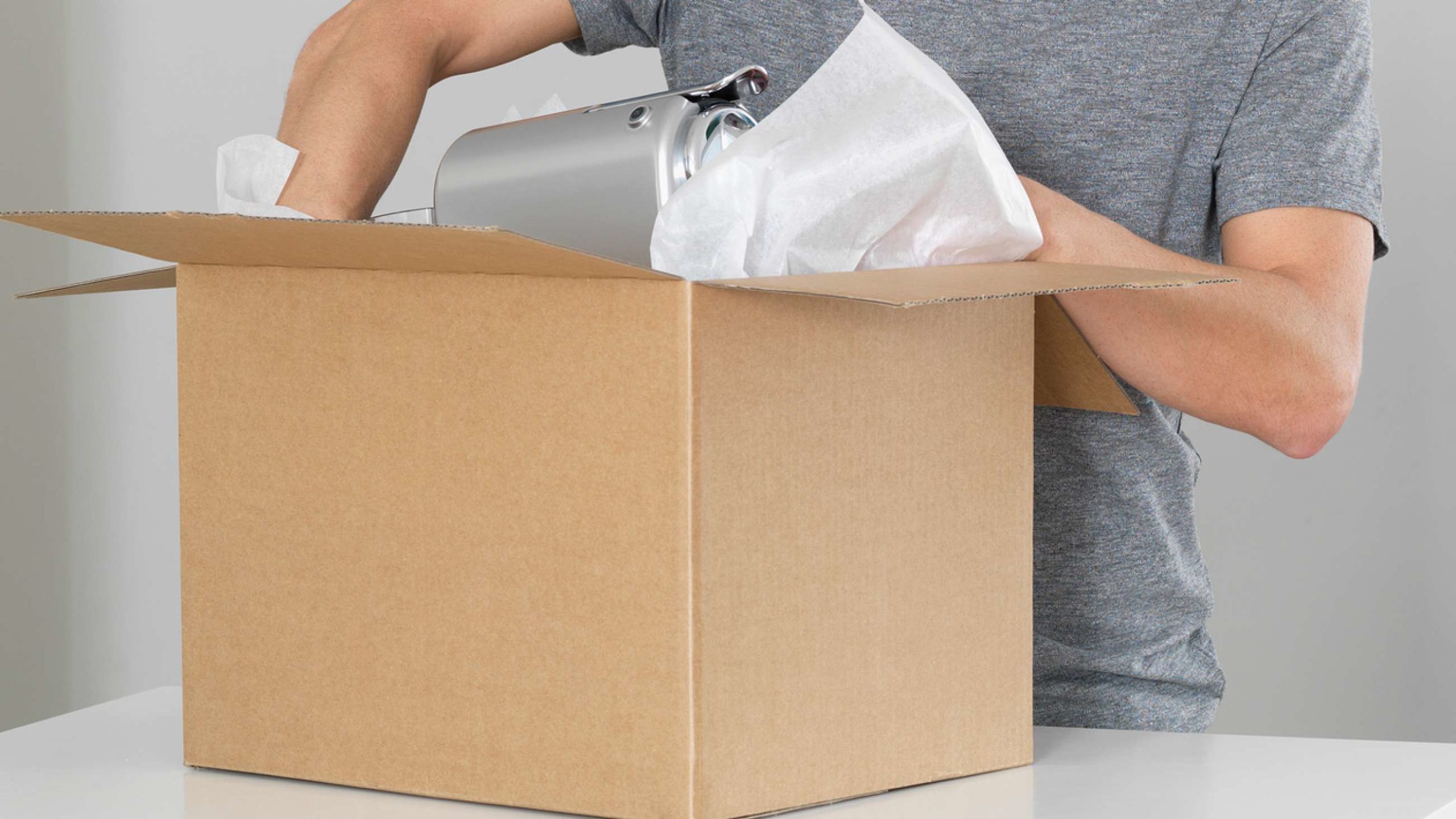
As an e-commerce business, package quality is a key element to success. If you want your customers to be satisfied with their purchase, you need to make sure your packages arrive in perfect condition every time. That’s why it’s important to have a system in place for quality control and assurance. In this blog post, we’ll look at how you can make sure your packages are perfect every time, so you can guarantee customer satisfaction and maximize profits.
The Importance of Quality Control
Quality control is an essential component of any successful e-commerce business. It ensures that customers receive products in perfect condition, free from defects, and delivered on time. It is especially important for e-commerce packaging since this is the first impression customers have of a product or brand. Quality control helps to protect against costly returns and refunds while providing assurance that orders are fulfilled accurately and reliably.
Quality control also helps to ensure that products are safe to use and meet all necessary safety standards. In addition, it ensures that the customer experience is positive, with no surprises when they receive their package.
Lastly, quality control helps protect businesses from reputational damage by ensuring customers get exactly what they expect from their purchases. By taking the time to ensure quality control processes are in place, businesses can rest assured that their products will be delivered in a timely and secure manner.
Why E-commerce Packaging?
E-commerce packaging is an important aspect of any business, especially if you are selling products online. With the advent of online shopping, it is more important than ever to ensure that your products arrive to customers in the best condition possible. Quality control is essential when it comes to e-commerce packaging, as it helps to ensure that all packages are properly sealed and labeled before they are shipped out.
E-commerce packaging can be a great way to differentiate yourself from competitors, as well as provide an extra level of protection for customers’ items. Quality control allows companies to guarantee that the packaging their products come in meets the highest standard. This not only ensures that customers’ items will arrive in good condition but also helps to give them peace of mind that their purchases are safe and secure.
In addition to providing a higher level of protection for customers, quality control service also allows businesses to maintain consistent packaging standards and reduce waste. By monitoring the quality of packages, companies can identify areas for improvement and implement processes to ensure that all packaging is up to a high standard. This helps to reduce wastage and improve efficiency, as well as helping to keep costs down.
What to Look for in a Quality Control Partner
When it comes to assuring quality and consistency in your e-commerce packaging, you need to look for a reliable partner who will help you make sure your packages meet the highest standards. Here are a few things to consider when choosing a quality control partner:
1. Expertise and Experience – When looking for a quality control partner, it’s important to find someone with extensive experience and expertise in the e-commerce packaging industry. Ask potential partners what type of experience they have working with e-commerce businesses, how long they have been in business, and what types of products they specialize in.
2. Quality Assurance Procedures – A good quality control partner should have strict procedures in place to ensure that all of your packages meet the highest standards. Ask what kind of procedures and processes they have in place to guarantee quality and consistency.
3. Packaging Solutions – Your quality control partner should be able to provide a range of solutions for your packaging needs. Ask about their capabilities for customizing, designing, and printing on different types of materials, such as corrugated cardboard, plastic, and foam.
4. Cost-Effective Pricing – Quality control doesn’t have to be expensive. Look for a partner that offers cost-effective pricing without sacrificing quality. Ask about their rates and any potential discounts or special offers they may have available.
5. Customer Service – As with any business relationship, customer service is key. Make sure you choose a quality control partner that is responsive, reliable, and willing to work with you to address any issues that may arise.
By finding the right quality control partner, you can rest assured that your e-commerce packaging will be perfect every time. Keep these points in mind when choosing a quality control partner to ensure your packages meet the highest standards.
How to Implement Quality Control in Your Business
When it comes to e-commerce packaging, quality control is essential. Without it, packages are more likely to get damaged or lost in transit and can lead to unhappy customers and costly returns. So, how can you ensure that your packages are always of the highest quality?
The first step is to choose the right partner for your e-commerce packaging quality control needs. You want someone who is reliable, experienced and knowledgeable about your particular industry. Once you’ve chosen the right partner, you’ll need to make sure that they understand your expectations. Explain exactly what you’re looking for and provide any necessary information about the products you’re shipping and the packaging materials used.
Next, you’ll need to establish an internal process for quality control. This should include inspecting each item before it’s shipped, checking for damages and defects, and making sure that everything is securely packed and labeled correctly. Your partner should also be able to inspect the items on their end, providing an additional level of assurance that your items will arrive in pristine condition.
Finally, consider investing in technology to help streamline your quality control process. Automated systems can check for defects, measure dimensions, and identify issues with labels or shipping addresses before they become problems. These systems can save you time and money by ensuring that packages are shipped quickly and accurately.
By implementing a comprehensive quality control system, you can ensure that your e-commerce packages are always perfect and ready to go out the door. This will help keep your customers happy, reduce costly returns, and improve the overall efficiency of your business.
Also Read: Reasons Why London Is the Ideal City for Business
Mistakes to Avoid When Implementing Quality Control
When it comes to e-commerce packaging quality control, there are a few key mistakes that should be avoided in order to ensure the quality of your packages is maintained. These mistakes range from not having enough quality assurance procedures in place, to not verifying the accuracy of your packaging materials. Here are some of the most common mistakes to avoid when implementing quality control:
1. Not having enough quality assurance procedures in place: Quality assurance procedures are essential for maintaining the quality of your packages. Without having the right procedures in place, you run the risk of letting errors slip through and compromising the quality of your packages. Make sure to have clear guidelines in place regarding your packaging processes, materials, and quality control inspections.
2. Not regularly inspecting your packages: Regularly inspecting your packages is a crucial step in ensuring that they meet the highest standards of quality. Inspecting your packages can help identify any issues before they become bigger problems. To ensure the quality of your packages, schedule regular checks and make sure all discrepancies are reported and fixed as soon as possible.
3. Not verifying the accuracy of packaging materials: It is important to verify that all packaging materials are accurate and up to date with the latest trends and regulations. Make sure to check the labels, sizes, and other materials used for packaging to ensure that everything is up to standard. This is especially important for international orders since different countries have different packaging requirements.
4. Relying solely on automation: Automation can be an effective tool in improving efficiency and accuracy when it comes to quality control. However, relying solely on automation can lead to mistakes and defects slipping through the cracks. Make sure to include human oversight and manual checks in addition to any automated systems you use.